There are some significant differences in design, material selection, geometric parameters and coatings between end mills for plastics and end mills for steel and aluminium, which are designed to suit the machining characteristics and requirements of different materials.
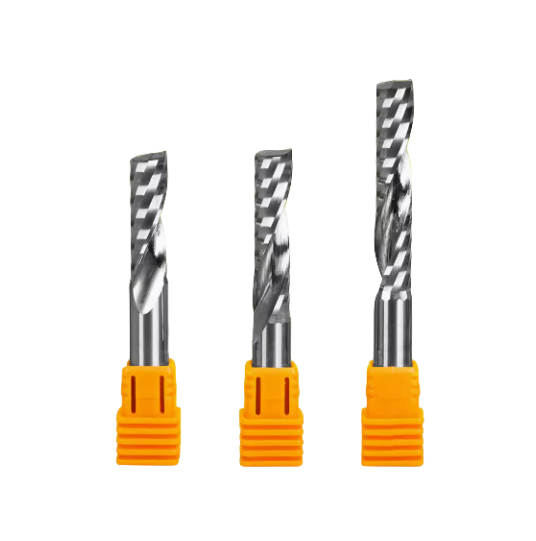
1. Material selection:
End mills for plastics are usually made of high-speed steel or carbide, sometimes with diamond coatings to improve wear resistance and extend tool life.
End mills for steel are often made of carbide, especially for those steels with high hardness, to ensure that the tool has sufficient hardness and wear resistance.
End mills for aluminium, on the other hand, may be constructed from tungsten steel, specifically designed for machining aluminium alloys, a material that has a low affinity for aluminium materials and helps to reduce tool sticking.
2. Geometric parameters:
End mills for plastics usually have large rake angles (γo = 25° to 30°) and back angles (αo = 18° to 20°) to reduce cutting forces and cutting temperatures and to prevent softening of the plastic and tool sticking.
End mills for steel may have smaller rake and rake angles to accommodate higher cutting forces and heat when machining metal.
End mills for aluminium, on the other hand, are designed with unique geometries to optimise chip evacuation and improve machining efficiency while reducing tool sticking.
3. Coatings:
End mills for plastics may feature special coatings to improve wear resistance and reduce friction for plastics machining.
Coatings for end mills for steel may be more focused on improving wear resistance and heat resistance to adapt to the high temperatures and pressures in metal machining.
Coatings on end mills for aluminium are designed to prevent material adhesion, optimise chip removal and improve cutting efficiency.
4. Tool construction:
End mills for plastics may prefer fewer flutes to facilitate chip evacuation and reduce clogging, especially when machining thin-walled parts or complex shapes.
Steel end mills may be designed to be more robust to accommodate the higher cutting forces that can be generated when working with metal.
End mills for aluminium may have special designs optimised for aluminium alloys, such as round bars with helical holes and optimised cutting edge shapes.
In summary, end mills for plastics differ significantly from those for steel and aluminium in terms of design and application, and these differences allow them to be better adapted to the characteristics and requirements of the materials they are machining.